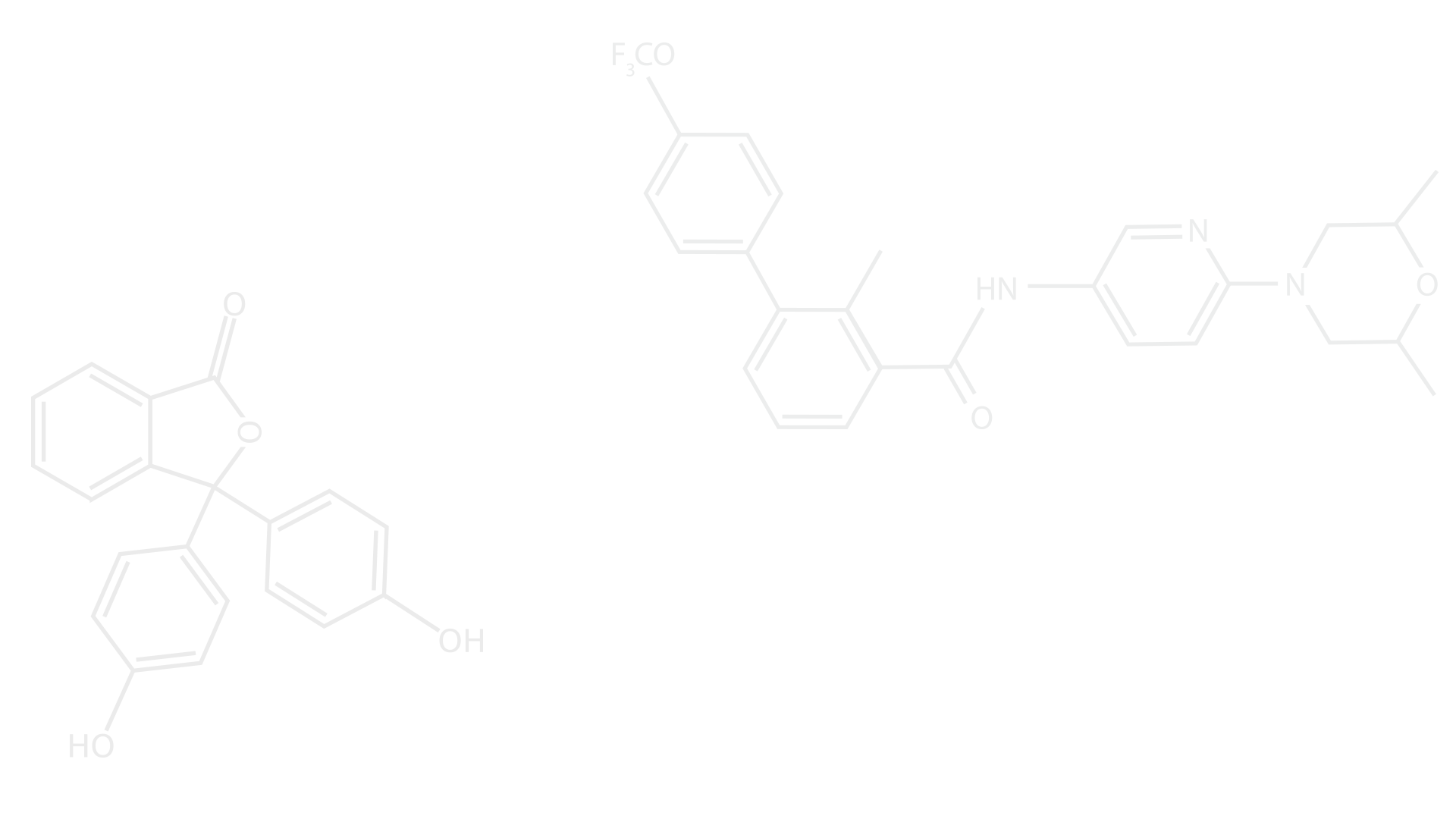
Sim's Electrical Companion
Cable Support
Knob & Tube
Knob and Tube was a commonly used method of wiring from the 1880's to around the end of the 1930's. Single fabric or rubber insulated cables were passed through and tied around ceramic tubes to erect the wiring system. The method includes the use of ceramic pulleys to tie cables around or change direction and tubes to pass through building fabric like joists or rafters. The primary causes for concern if you discover this still in service is the insulation is likely to have become brittle and be no longer viable. There is NO earth and Line and Neutral were often not identified. Though often considered to be of antique age I have found active knob and tube systems. Houses older than 90 years often have remnants of it in their loft spaces or under the floorboards.

Bare Conductors
Conductors can be installed devoid of insulation in some circumstances. Examples include Bus bars, overhead power lines, substations and power track lighting systems. All need to adhere to regulations to provide adequate protection for safety and fire risk. It was once a practice to install bare wires for final circuits in houses laid into wooden troughs. This obviously was not fashionable for long as it burnt many a house down. Self supporting suspension cables need to be installed at height of at least 6m in agricultural or horticultural premises.
Bare conductors can be in place where the personnel are electrically instructed persons and there are sufficient barriers (obstacles) in place or placing at height.

Clipped Direct
Clipped direct - this method relies on the cable being away from any dangers or of sufficient cross sectional area for it to have reasonable amount of mechanical strength. Nowadays it is not acceptable to clip single current carrying cables. Single cables can be installed for earthing, bonding and supplementary bonding. The minimum csa for a single clipped direct cable is 4mm².

Buried
Buried cables and their connections should be designed for that purpose or be in containment that can be used in that way. Buried communication cables should not come within 100mm of any buried power cables. Where cables are buried it should have cable indicator tape 100mm from the surface.

Cable Ladder
Used for providing strong cable supports for heavy duty cables. It has a wide variety of bends, tees, angles reducers and enlargers to allow for a great variety of installations with little need for bespoke design and cutting.

Conduit
​
PVC (Poly Vinyl Chloride) Conduit
Black, white or red are the most common colours, others are available but more specialist. light and heavy guage. Heavy guage is more expensive but produces far superior bends. Flexible PVC conduit can be used where vibration or complicated runs are involved. White PVC Conduit should not be used outside or where it may be subject to ultraviolet light as this degrades the PVC.
Steel Conduit types
Black Enamel
Painted enamel finish - Cuts and threads need to be sprayed or painted to avoid rusting.
Zinc Galvanised
Cuts and threads need to be zinc sprayed to maintain its resistance to rusting.
Sheradised
Heat treated zinc application very resistant to rust.
Stainless Steel
Very expensive, highly decorative and resistant to chemicals and rust.
Flexible Steel Conduit
Flexible steel conduit for complicated runs or for vibration resistance.

Conduit Cable Factors
To ensure cables are not subject to damage by overheating conduit systems cable should not occupy more than 60% of the internal space in the conduit. To determine this firstly add up the cable factors for all the cables intended to go in the conduit using the table:
​
Example:
If you had 8 x 6.0mm² cables the factor would be 8 x 58 = 464
​
Then you pick a conduit that has a higher value than that to suit depending upon its length (left column) and how many bends it has in it. To determine what you can safely instal use the tables below. The table is suitable for conduit sizes up to 32mm diameter. For 38mm use 32 factor x 1.4 ; for 50mm use 32 factor x 2.6 ; for 63mm use 32 factor x 4.2.
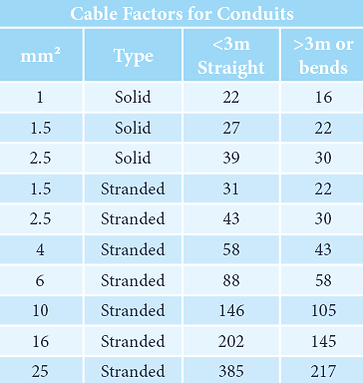

Containment - Ducting & Trunking
​

Ducting & Service Tunnels
Ducts are used to carry cables underground or through building fabric. Ducts have a minimum diameter of 32mm. Ducts may be colour coded to identify what they contain e.g. purple for communications and fibre-optic. Ducts allow replacement of old cables or addition of new services without having to dig down to them. Minimum depths: 450mm below gardens; 750mm below roads; 1000mm below agricultural land.
​
Service tunnels allow the cables to be supported and to allow air flow over them. Additionally maintenance or additions are more easily achieved. Substantial service tunnels in the UK include interconnectors, channel tunnel, River Medway (Kent) and Dartford tunnel services.
Trunking
Available in PVC, Lighting specific, Dado, Skirting and steel varieties. Steel can be used as the protective conductor presuming it is confirmed to be of sufficiently low impedance to the main earthing terminal. Similar to conduit systems there is a mathematical method of ensuring a specified trunking system will hold the required amount of cables and be compliant. 65% of the trunking needs to be free of cables to comply. The likelihood of future additions or alterations should be taken into account. To determine if the cable will fit you need to work out how many cables and of what csa to determine the total cable factor based on the table left.
Once this has been determined you can select trunking that has a greater figure than the calculated cable factor.

Example:
If you have the following cables:
20 x 2.5 mm² solid thermoplastic
15 x 4 mm² stranded thermosetting
30 x 6 mm² stranded thermoplastic
12 x 10 mm² stranded thermosetting
​
The calculation would be
20 x 11.9 = 238
15 x 18.1 = 271.5
30 x 21.2 = 636
12 x 36.3 = 435.6
​
238 + 271.5 + 636 + 435.6 = 1581.1
​
The cables would fit in trunking:
75 x 75; 100 x 50 or larger.


Bus Bar Trunking / Ducting
Bus bars are (usually) uninsulated copper bars for distribution of electrical energy. They are raised on insulators and installed in bus bar trunking and enclosures. The trunking is usually metallic for mechanical protection. As such the trunking system will be carefully designed to ensure the containment does not come into contact with live conductors.
Bus duct systems are for a wide range of power distribution requirements between 100 - 6500 Amperes. It is highly adaptable and useful where distribution modifications are likely e.g. in an assembly line in manufacturing where processes are regularly updated or changed. The navy use this system of distribution on military ships and boats for similar reasons.
Power Track Systems
Power tracks provide the end user with an adaptable system for lighting or power distribution. Exhibition halls, shop displays and factories make use of them where power and lighting requirements vary significantly throughout the installations lifetime.
​
Though mostly the realm of commercial and industrial applications some simple, low voltage and Extra Low Voltage (ELV) versions have been manufactured for domestic use.

Cable Basket or wire mesh cable tray
A simple method of supporting cables without the need for additional fixings. Used extensively for information technology where there are large volumes of communications cables. Very easy to add new circuits compared to a closed system like trunking or conduit.
Its wire frame construction makes allows air to flow around installed cables reducing any loses due to heat. Designed to clip together it as a fast lightweight solution for cable management where modifications or additions are likely. A good example would be a server farm or in a manufacturing plant.
​
Cable tray
A relatively low profile method of supporting cables this flat perforated metal is designed to be suspended from the building fabric. This improves the circulation around the supported cables. Available in a wide range of sizes from 50mm to 1000mm. Available in a variety of materials like resin for outdoor application, aluminium for light weigh metallic applications. Stainless steel for corrosion resistance or for trendy wine bars! The most common by far is galvanised perforated tray. Note cuts in galvanised tray need to be sprayed to maintain the corrosion resistance of the zinc coating.
​
Cables are secured the tray with cable ties these need to be metallic if the tray is facing to the floor to prevent danger of entanglement in the case of a fire. The power cables should each be a cable width apart to allow circulation. The down side of this and nearly all containment system is additions and alterations are often added with out taking this spacing factor into account. Band I and Band II cables should not be run next to each other or cross each other.
Containment Classifications BS7671
​
Reference Method A-F
How a cable is contained or supported through its run is called the reference method. When a designer is planning an installation the method needs to be taken into account as it can affect the performance, life and safety of the installation. The categories can affect a cables performance significantly. For example a cable surrounded by thermal insulation may lose half of its current carrying capacity. For greater detail on reference methods see Appendix 4 of BS7671.
Reference Method A
​
Contained in conduit within a thermally insulated wall. The conduit should be touching the inner surface of the wall to allow heat to be drawn away from the cable. This method also applies to single or multi-core cables in the wall not in conduit. Other less commonly used methods include non sheathed cables in Architrave mouldings, door or window frames.

Reference Method B
Single or multi-core cables contained in trunking or conduit that is either suspended or attached to walls or ceilings. This includes flush floor mounted & suspended trunking e.g. lighting trunking. Other applications include in a suspended ceiling and within non insulated voids or ducting.
Reference Method C
Clipped Direct. As the name suggests this is where containment is not used and the cable is directly fixed to the fabric of the building. The cables may be single or multi-core cables but single cables must only be used for protective purposes like Bonding for example. The cable should be adequately supported by the building fabric but not touching insulation. Reference C is also used for cables embedded in the building fabric provided it is not embedded in the insulation. E.g. Brick, block or plaster walls.
Reference Method D
Multi-core armoured cable in ducting or conduit buried in the ground. This can apply to cables directly buried with additional protection of armour or capping material normally stone. Buried cables should be laid on sifted sand and covered with sand to avoid damage to the cable when back filling. Additionally the depth is dependant upon the land use. Usually ≥0.6m with mechanical protection and cultivated areas 1m or greater.

Reference Method E
​
Multi-core cables supported on perforated or non perforated cable tray or ladder. Table 4C4 BS7671 gives greater detail on requirements for this installation method. Cables should be separated.

Reference Method F
Single cables supported on perforated or non perforated cable tray or ladder. Table 4C5 BS7671 gives greater detail on requirements for this installation method. phases should be together as should line and neutral conductors. Only bonding conductors can be individually installed.

Reference Method G
Bare or non sheathed cables in free air. See the tables in Appendix 4 BS 7671 for details. Vertical cables carry significantly less current due to heating effects at the top of the run. Example use pole mounted power supplies.
Reference Methods 100-103
​
"Yes I know they have changed from letters to numbers! Bless the IET for confusing matters!"
Reference to Table 4A2 BS7671 will make matters clearer.
Reference methods 100 - 103 concern cables that come into contact with thermal insulation. The key problem with this installation method is it reduces the cables current carrying capacity due to heating effects.
Reference Method 100
This applies to cables in less than 100mm of insulation E.g. in loft spaces before the building regulations increased the insulation required. Houses that were insulated in the loft space used to only have about 100mm of insulation so this applies to lighting circuits in most of the houses in the UK. Cables must be touching the free air or thermally conductive surface.

Reference Method 101
This applies to cables that are attached to the building fabric but have more than 100mm of insulation on top of them. Houses recently insulated in basic insulation will fall into this category. Cables must be touching the free air or thermally conductive surface. If loft access is unlikely for anything other than inspection this is quite common and cheap way to improve a buildings thermal efficiency but creates difficulties for safe access and working.

Reference Method 102
This method applies to cables covered in thermal insulation & boarded up for safe roof access / storage or conversion. As fewer people can afford to move they are often modifying the building they already have. For example moving into the loft space. Cables should touch the inner surface of floor or ceiling. Consideration should be made by the designer that boarding over is likely and may be retrofitted after the construction of the installation.

Reference Method 103
This method applies to cables concealed in walls and surrounded by insulation. Not touching the inner leaf of wall / plasterboard. This is the most limiting method of installation and has the effect of halving the current carrying capacity of the cable.
Often in domestic lighting this will not affect the choice of cable but higher power circuits can be seriously affected.
​
Example: a shower circuit fed from above and encased in insulation it may be impossible to install a sensible cable size.
A 9.5kW shower will draw 9500/230 = 41 Amps. In insulation the cable capacity is halved so you would need a cable to withstand the equivalent of 82 Amps! A 16mm2 cable can only carry 42.5A in Ref 103. Table 4D5
