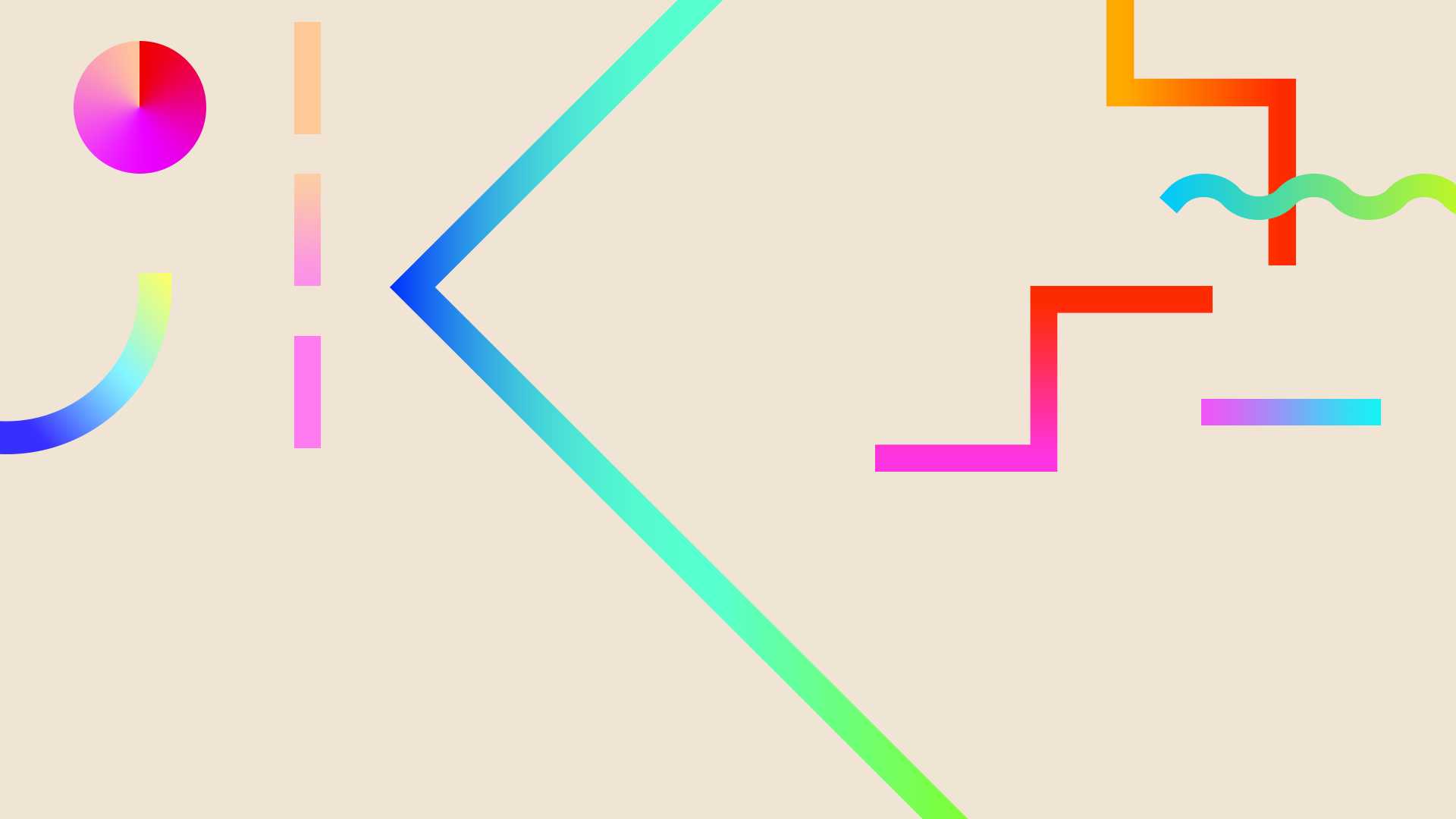
Sim's Electrical Companion

Health & Safety at Work Act - 1974
​
In 1974 the Health and Safety at Work Act (HASAWA) was introduced to reduce accidents and occupational health complaints due to working conditions. The primary concern of the act was to make clear the responsibilities of both employers and employees with regard to health & safety. The Act is statutory (LAW) and as such breaches of the legislation can result in prosecution. The act is the responsibility of the Health & Safety Executive (HSE) and is enforced by the local authorities.
​
The Act is considered to be an umbrella act. This is because under its confine are more focused regulations including personal protective equipment, working at height or in confined spaces, working with chemicals, hazardous materials, electricity and many more working scenarios considered to a specific danger. Some of these sub Acts are briefly described in the sections below. Greater detail can be found on the UK .gov website.
The Employers Responsibilities
​
The employer has a duty to ensure the working environment is a safe and has adequate welfare facilities. These includes: Washing, cleaning, toilet facilities, a safe place to consume food, rest rooms, facilities for nursing or pregnant mothers and protection of non-smokers from tobacco smoke. Facilities on site for smokers is not a requirement.
Much of this is now taken for granted but it has not always been the case. An example of poor health and hygiene practises in the recent past was the plight of coal workers to have safe working conditions and welfare facilities.
​
Additional responsibilities include the provision of training where required so staff are competent in their duties including the use of work equipment and facilities. Health and safety training must be given by a competent person and be free to all employees. Equipment required to achieve tasks safety like personal protective equipment (PPE) or manual handling aids must also be provided free of charge.
​
The Employees Responsibilities
​
The employee is responsible for taking care of his/her own personal safety and of others that may be affected by their actions or omissions. This places the blame squarely at the feet of the employee if laziness or deliberate acts end in an accident.
​
If the employee is given equipment to achieve a task safely e.g. a lifting aid or personal protective equipment it is their responsibility to use it properly. Items provided for these purposes should be replaced if they are no longer fit for service.
Safety Policy
If the employer has five or more employees the employer must produce a health and safety policy outlining how they achieve and maintain compliance with HASAWA. The policy outlines who the duty holders are and lists their responsibilities with regards to health, safety, welfare and training.
​
Actions and arrangements are to identify where to find specific information relevant to the section. These may include indications on where to find risk assessments, permits to work, safe systems of work, training policies, first aid, emergency and evacuation procedures and any required planning for intended future changes to work functions. This indicates forward planning and a strategy for maintaining a safe working environment.
​
A poster should be placed a prominent position outlining the main points of the legislation where staff can read it. First aid equipment and the location of the accident book should be included in the statement.
The policy is deliberately easy to understand and should be accessible to all employees, contractors and visitors.
Failure to provide a health & safety policy where required can be sanctioned by fines, imprisonment or disqualification.
​
A copy of a blank policy can be obtained from the .gov website:


Management of Health & Safety at Work Regulations
In 1999 the management of Health & Safety at Work Regulations were drawn up to assist employers in the implementation of their health & safety policy. The regulations give clear instructions on methods of achieving the goals set out in the policy document.
The roles of line managers and supervisors are to ensure that employees follow guidance given in company policies. These include risk assessments, compulsory training, emergency procedures and any other policies relevant to the application of the health & safety policy.
​
Risk assessment is a major part of effectively managing company health and safety. It is an ongoing process and should be regularly reviewed to ensure the risk has not changed and the management of that risk is still sufficient to keep persons from harm.
​
Even a small firm working in a domestic premises will need to risk assess before starting work. The risk may not seem great in this scenario but the reality is there is risk in every work place especially when it has not been considered. Examples of risk in this seemingly safe environment include:
​
Working on or near asbestos. Asbestos was banned in the UK in 1999.
Work at height - loft access, ceiling lights or hatch cutting for cable runs.
Live electricity - During live testing, installation or fault diagnosis.
Confined spaces - Working in loft spaces, under floors or in excavations.
Unprotected drops, fragile roofs, lifted boards & un-boarded loft spaces.
Children & animals - Their unpredictable nature can be a significant risk.
The risks are significant but when sufficient control measures are implemented the risk level reduces significantly or is removed entirely. The application of a generic risk assessments requires a review in every property as the risk will be different and the assessment may need modifying to acknowledge that.

There may be additional risks like unprotected drops in partially built properties fire or shock risk due to renovation work etc. The possibilities are endless even in something we consider so simple like a domestic setting. The level of risk can be determined using a traffic light system like the one pictured where the probability or likelihood of an accident occuring would be multiplied by the level of impact or severity of the potential hazard.
​
Personally I would rather just describe the potential hazard and the method of reducing or negating the risk. What ever the method chosen it should be easily understood and employees should know where it is stored.
​
Example control measures include; Safe isolation, use of barriers or locks, employee training, supervision, use of PPE, provision of access equipment, use of safe systems of work or method statements, permit to work systems, removal of services etc.
​
Further control measures recommended in the risk assessment - the time period for application should be reflective of the level of threat.

Method Statements & Permits to Work
Where a work function requires a risk assessment a method statement may be required to inform staff on how to achieve the task safely. Like risk assessments the method statements or safe systems of work should be reviewed to ensure they are still effective and relevant. The Method statement will highlight the risks and then detail the control measures required to mitigate the risk. The document is non-statutory but it may be used in a court or tribunal to demonstrate the companies intention toward maintaining a safe working environment. It may also be used in their defence in the case of an accident where the system has not been effective or was not complied with.
​
Permits to work
​
A permit to work form is issued to persons that are undertaking work that has a highlighted element of risk. Permits to work are normally reserved for sub contractors. Though it may be company policy for all employees to use the process. The permit would be issued by an instructed person who has knowledge of the companies policies, procedures and nature of the risks. Issuing the permit will be the time to state the companies policies to the person/s that are undertaking the work.
​
Examples of work activities that commonly require a permit to work include:
Hot works - e.g. Soldering, lead work, flat roofing or welding.
Roof access - especially where there are unprotected drops or fragile areas.
Electrical work activities - e.g. live testing, inspection or fault finding.
Solo working or work in confined spaces.
Working with dangerous chemicals, gases or explosive atmospheres.
​
When a permit to work has been issued it is standard for the person conducting the work to return the form for a counter signature upon completion of the work. In the case of hot works it would usually be a requirement for the area that the hot works was conducted in to be supervised for at least an hour to ensure that there is no danger of fire. Some companies require a hot works area to be supervised for three hours after completion of the works.

Work at Height Regulations 2005
Work at height is considered to be any work taking place above a solid level. This may only be a few inches but it would qualify if there was a possibility of injury. This may include unprotected drops, use of access equipment or working on fragile roofs or unboarded loft spaces or ceiling voids.
​
The Regulations require work at height to be properly planned and organised. All operatives should be trained in the use of any required access equipment or be properly supervised by competent persons. risk assessments and method statements where required should be maintained and made accessible to all operatives involved in that operation.
​
The choice of access equipment should be appropriate to the task. It should be noted that ladders are considered to be access equipment and NOT working platforms. Only very light short duration work may be done on an appropriate type of ladder.
​
Fragile surfaces and roofs need to be highlighted and if possible appropriate barriers put in place to avoid accidental access. Some fragile roofs may be accessed using crawl boards. If this is the case ensure they are supported at both ends and are secured to prevent slipping. In some cases Access equipment may be required.
​
All work at height should be risk assessed and if deemed necessary a safe system of work should be established. All persons needing access to that area should be trained and have read & understood the associated method statements and risk assessments. Permits to work may be required for roof access, confined spaces or work around unprotected drops or in trenches/excavations.
​
Where it is not possible to avoid working at height methods should be put in place to minimise the risk of a fall or the consequences if a fall does occur. Scaffolding is used to access areas at height and provide a temporary safe working platform. Another method is using a fall arrest harnesses where scaffolding is not possible e.g. inspection of motorway bridges. Another method of ensuring the survival of a person who falls from a height is to incorporate safety nets like those used by practicing trapeze artists.
Ladders & Steps
Contrary to popular belief ladders and steps are only for access and inspection or brief spells of light work. They should only be used for very short durations ideally less than 30 minutes and not for heavy physical work. Ladders and step ladders are attributed to cause a third of all reported injuries and deaths from height.
​
The HSE has written a guidance document on safe use of ladders and step ladders. The most important points of which are highlighted here.
​
First and foremost the ladder or steps should be thoroughly checked to ensure they a fit for purpose before use. An organised company will have a register for their access equipment which should highlight the equipment available and its storage location. Check on the side of the equipment to see if there is an inspection check list.
​
You should include the following checks:
Wooden ladders should be unpainted as this could hide damage.
Check that the feet are present and made of a non-slip material.
Shake the steps to hear if there are any loose sections.
Ensure supports are effective, undamaged and move freely.
Inspect the rungs and look for signs of damage or loose fixings.
To determine if a ladder or steps are suitable they must be able to reach the area required without the user over reaching. You must not stand on the top rung, work off the side of steps or over reach. The optimum angle for using a ladder is 75 Degrees. This is equal to one in four as shown in the illustration left.

When used to access a platform the ladder should extend at least one metre to provide a safe hand hold until you have stepped off from the ladder. The ladder should be secured to the wall upper rail or at its base to prevent it sliding down the wall under load. During the process of securing it you can use a person to 'foot' the ladder.
​
To do this hold both stiles with your hands keep one foot on the ground and one on the bottom rung to support the ladder during setting up or for short duration inspections.
Ensure the ladder is on a level non slip surface. Never use a ladder off of a surface that is not the ground. Do not stand on the top rung. Use three point climbing technique when ascending or descending ladders for optimum safety.
Access Equipment
A mobile scaffold is designed to be erected without the need for tools. They can be up to 12 meters.
​
The main components are:
Toe boards - Used to prevent items from being kicked off the walk-board potentially causing harm.
Walk boards - Safe platform to work on. Incorporating a hatch for safe passage on to the platform.
Horizontal braces - Use for improving rigidity and as a safety barrier on the working platform.
Internal fixed ladder - for ascent/descent to platform level.
Cross braces - Provide structural stability.
Out riggers - Used to increase the base area so the tower can be raised to a greater height.
Castors - Used for moving the scaffold tower into position. Brakes are incorporated on all four.
​
There are many different types of scaffold tower including ones that have a cantilever designed for working over the top of something. Whatever the design all towers must be erected and struck (taken down) by a competent trained person. The easiest way to prove competency is to hold a license for the particular type of scaffold you are working on. Most companies will insist on seeing proof of your competence in order to assemble or strike a tower. The Prefabricated Access Suppliers and Manufacturers Association (PASMA) is one company that can provide training & issue licences that are recognised nationally. The licence needs to be renewed every 5 years to ensure you are not developing bad habits or practices. This will also allow updating to latest regulations that may have been introduced.
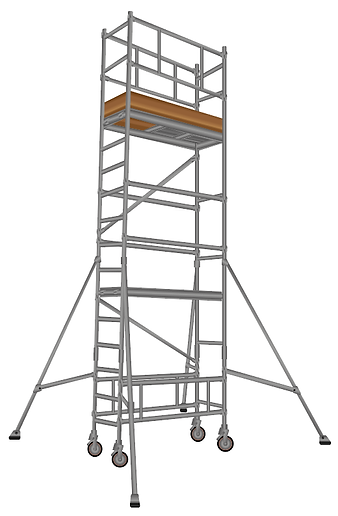
Requirements & recommendations from The Health & Safety Executive (HSE). At all times manufacturers instructions should be followed. The tower must never be erected with missing or damaged parts. Towers above 2 meters have to be inspected upon erection and within seven days thereafter by a trained competent person. All inspections must be recorded and a tag installed onto the tower scaffold. If necessary inspection records should be made available to the HSE.
​
During erection and dismantling the through the trap method should be used for removing components above the working platform. This method ensures the trap sides are acting as a safety guard rail. Never climb on the outside of a tower. The ladder should be used within the tower. Harnesses should not be used on mobile towers as they are restrictive and would not allow a leap of faith in the case of a collapse.
​
The maximum height used to be determined by a 3:1 rule where the height could be no more than three times the smallest base dimension. This is now not the case and for all towers, manufacturers instructions should be followed.
A tower should not be used in strong winds or be subject to any other form of side loading. Towers should not be used in any other adverse weather especially rain, lightning storms, snow or icy conditions. Predicted winds above 40 mph require the tower to be dismantled if it is safe to do so. If a tower is higher than 5m it should be secured to a solid structure. When a tower is being moved it should be struck down to a maximum height of four meters. No person should be on the tower during moving operations.
Mobile Elevated Work Platforms (MEWP)
These work platforms are mobile powered access machines. The two basic types are vertical lift or boom types (Cherry pickers). The vertical lift platforms are often scissor lift types though ram types are also available.
​
International Powered Access Federation (IPAF)
​
Is a not for profit organisation that has in its membership 85% of the worlds MEWP's. Their purpose is to maintain safe and effective use of MEWP's worldwide. They provide training and information for platform users. They have a membership scheme and provide Powered Access Licence (PAL) cards to individuals who have successfully completed one or more of their training courses. The PAL card is similar to a driving licence in the sense that it only grants the holder permission to use the category of platform they have been trained on.
The categories of platform are:
Classification - Types of MEWP
​
1A Static Vertical
This is a vehicle mounted platform that can travel vertically only. Note the vehicle must be stationary during use.
​
1B Static Boom
This is a cherry picker type machine that is not drivable. It may be mounted on a vehicle but the vehicle must not be in motion while the boom is in use. Sometimes called spider type because of the stabilising leg design.
​
3A Mobile Vertical
This vehicle can be driven but the platform only travels vertically.
​
3B Mobile Boom
This is an access boom that can be driven.
​
PAV Push Around Vehicle
Push Around Portables need to be manually pushed into the location where it is needed before use.
​
H Harness
Harness or lanyard training required.
​
SPECIAL
As suggested by the name the working platform is designed for a specific task which requires training that is not covered by one of the other existing licence types.
​
MCWP
Mast Climbing Work Platforms are long working platforms that climb a central mast. They are becoming more common for construction access as they can remove many of the requirements for scaffolding as courses of a building are laid.
IAD
Insulated Aerial Devices are specialist machines that allow operators to work on or near live conductors. They can be used to make repairs to power networks without isolating the power first.
​
MM MEWP
Designed for managers or foremen that work around MEWP operators.

Confined Spaces Regulations
A space is considered to be confined if it is reasonably enclosed or has limited means of escape and has a level of risk associated with it. Risk could be defined as entrapment, collapse, asphyxiation, carbon monoxide poisoning, electrocution, drowning, exposure to gases or extremes of temperature, fire, explosive atmospheres or any other effect that may be considered a risk. A risk assessment should be conducted to assess any requirements that would mitigate or remove the risk.
​
In my career I have worked in many confined spaces to conduct electrical work. This is why I have assembled this page to inform the reader on the regulatory requirements. Examples of where electrical work may be undertaken include:
Loft spaces or roof voids, plenum chambers (air conditioning plant), ducting, trenches, voids between walls or floors, service tunnels, risers, plant rooms, sewers, catacombs & intake rooms.
​
To see the extent of your responsibilities when working in or employing people to work in confined spaces see the Approved Code of Practice on the .gov website Common Applications of the Regulations.
​
When working around explosive atmospheres due to stored materials or explosive gases like in sewers or catacombs. A method of detecting gas should be employed. Thankfully we have relatively cheap devices now rather than using a budgie as was the old method.
A method of communication or buddy system should be employed so someone always knows where you are and can maintain contact or assist in an emergency.

Where gases are expected Breathing apparatus may be required and rubberised equipment or beryllium copper tools to limit the possibility of creating a spark. Other harmful gases include Carbon Dioxide or Carbon monoxide both of which can in high concentrations kill a human if they do not have access to an adequate oxygen supply. The symptoms of carbon monoxide poisoning can be very similar to flu like symptoms without the fever they include: Nausea, short breath, dizziness, headaches and difficulty breathing. Extreme cases are fatal around 50 deaths are attributed to carbon monoxide poisoning in the UK per annum.* Other regulations apply to specific confined spaces like working in mines, diving or aboard sea going vessels.
When working below ground there is an added danger of water causing collapse of walls or ceilings so these should be properly shored up before any installation work can take place. Work in trenches lower than 600mm requires battering of the walls to prevent collapse as pictured right.
To prevent accidental falling into the trench barriers and signage should be used. Another method is to slope the sides to at least 45 degrees to prevent accidental collapse. If the excavated material is very loose or wet a lower angle will be required.
Safety Signs & Signals 1996
Mandatory Signs
​
Blue circular signs with a white pictogram and white border are mandatory notices. Passing these signs without conforming to their meaning is a health and safety offense. At the entrance to every UK construction site will be mandatory signs indicating that beyond that point Hard hats, reinforced boots and a high visibility vest must be worn.

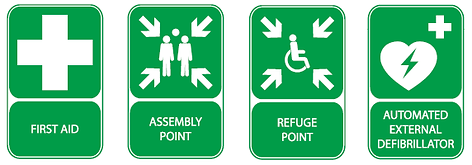
Safe Condition / Information Sign
These signs are rectangular or square with a white pictogram or text on a green background. Common uses include fire exits, refuge points and first aid stations. Push bar to open signs are covered by separate legislation.
All public buildings and workplaces must indicate their exit passageways and stair wells that lead towards a fire exits. Private dwellings do not require such notices however the common ways of multiple occupancy housing and flats do.
Prohibition Signs
Red circular signs with White pictograms or text and a diagonal cross bar in red. These signs indicate activities that are not allowed in the areas they are placed. The most ubiquitous of which would be the all too common no smoking sign.
​
Similar to mandatory signs failure to comply with these signs is a breach of health and safety law and may have heavy sanctions attached to non compliance.
Hazard Warning Signs
Yellow Triangle with a black border and black pictograph or text indicates a warning or hazard. Often an exclamation mark indicating caution will be next to another sign with more information on the nature of the hazard or warning.



Safety Signs & Signals 1996
Fire Safety Signs
Signs for identifying apparatus for the purpose of fire fighting or raising the alarm use a white pictograms on a red background.
​
Unlike prohibition signs they are on a square or rectangular background with a white border. In some cases signs are not required if the equipment is bright red e.g. call points for raising the alarm. The pictograms are mandatory and text may be added or omitted.

Fire action signs are mandatory in public buildings like hotels or hospitals for example.

Hand Signals
​
As well as safety signs hand signals are also covered by the Health & Safety (Safety signs and signals) Regulations. The signals must be easy to do and clear to understand. Operations that require the use of hand signals for safety include directing crane operators and site traffic.
Hand signals are also commonly used by seamen, policemen, traffic officers, divers, banksmen, engineers, train conductors, crane operators, flight decks and airports.
​
Props may be used to make the signal clearer like flags lights or beacons.
Extensive signalling like semaphore has its own regulations. The International Code of symbols covers flag hoist, semaphore, signal lamps and radiotelegraphy.
Example signals include but are not limited to:
​
Start Indicate the start of a command.
Stop Interrupt or end a movement.
End Stop the operation.
Raise To have a load raised.
Lower To have a load lowered.
Forwards To be coordinated with the corresponding hand signals.
Backwards To be coordinated with the corresponding hand signals.
Right To be coordinated with the corresponding hand signals.
Left To be coordinated with the corresponding hand signals.
Danger For an emergency stop.
Quickly To speed up a movement for safety reasons.


Control of Substances Hazardous to Health (COSHH)
The COSHH Regulations refer to any chemical or material that may cause negative effects to living organisms. The COSHH Regulations refer to workplace exposure and require that an assessment be made on every chemical and material that may cause a health hazard however minor it may be.
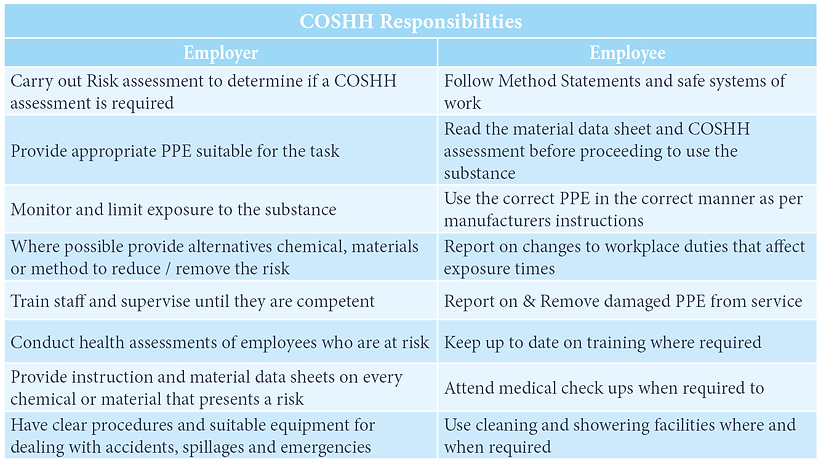
Hazard Symbols
​
Any chemical or material that bears one of the pictured symbols needs to have a material safety data sheet (MSDS). The MSDS should be kept in a location near where the substance is stored and is accessible to workers that use the substance.
COSHH Warning symbols have been changed since 2017 from an orange and black square symbol to the current nine symbols with black and white pictograms in a red diamond border:

Health Hazards or Caution
​
Usually not found on its own this symbol is designed to grab the users attention and encourage you to look for more information. May cause irritation, burns, drowsiness, dizziness irritation or damage to tissue or the environment are examples.
Correct manual handling aids should be used when transporting compressed gasses. Emergency procedures must be understood and implemented in the case of an unintended release of gas.
De-pressurising gasses causes large scale expansion & cooling this may cause cryogenic burns if in contact with live tissue.
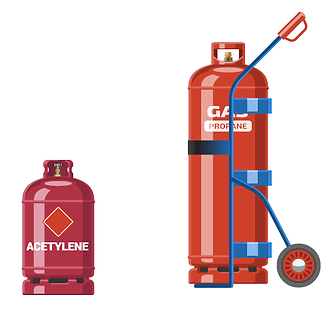
Pressurised Gases
​
Any gas under pressure can be an explosion risk if they are not stored and transported correctly. I have personally seen a CO2 cylinder break through a wall when it fell and knocked off its valve head. Most gas cylinders need to be stored upright and secured into place.


Flammable
Warning that the material has a low flash point and may catch fire with even a brief source of ignition e.g. a spark. Flammable products should be stored in their correct container and in an area away from sources of ignition. Flammable chemicals are usually stored in metal cabinets or specialised containers. This sign replaces the previous versions of Flammable and highly flammable.
​
Oxidising
The substance has a strong reaction with air and may cause fires or explosions in the process of reacting. During the reaction oxygen and heat are produced so only fuel remains to cause fire. As such it should be stored away from flammable materials and treated much the same as flammable substances.
​

Explosives
This is a caution that the material or substance is explosive and should be handled with care by an instructed person. It must only be used for the purpose for which they were designed. Storage must be in line with the manufacturers’ direction. Reference should be made to the Material Safety Data Sheet to ensure all precautions are taken and adequate provision has been made for emergency situations.


Corrosive
This applies to either living tissue or other materials. The substance can cause burning and dissolves some materials. Care should be taken to ensure it does not come into contact with any materials it reacts to in an uncontrolled way. In many cases the gases given off during this process are caustic and may cause breathing difficulties. Accidental contact with some substances may also cause fire or explosions.
Hazardous / Harmful to the Environment
Any substance that can cause damage to the eco system. Storage of these substance must be strictly designed to remove the risk of accidental release in the case of spillages. Areas where these chemicals are stored should be tanked and have appropriate spill kits and methods of disposal. Accidental release must be reported to the environment agency immediately.

Toxic
This has been reclassified and now includes substances that are toxic and very toxic. This applies to any substance that is harmful when in contact with skin, eye contact, inhaled or in-gested. Relevant Personal Protective Equipment (PPE) & Respiratory Protective Equipment (RPE) should be located near the storage location. This notice is applied to substances that need very small amounts to cause harm. Some materials that are toxic in large volumes will not carry this symbol.
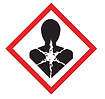
Serious Health Hazard
Any substance that is a great threat to human or animal life. Includes acids, alkalis, carcinogens etc. May be fatal or cause long term health problems or genetic defects.
Any Substance that bears the symbols above will need to be risk assessed and have a material safety data sheet detialing the exact nature of the hazards and prescribed precautions for use. See the next page - Material Safety Data Sheet and COSHH assessment.
Material Safety Data Sheets (MSDS)
For every chemical used in a workplace there should be a risk assessment conducted to determine the level of risk it presents to persons, livestock or property. The main risks presented by a product will be listed on its Material Safety Data Sheet. This should be accessible to all persons that use the product and be stored local to where the material or chemical is stored. Material Safety Data Sheets are often made available through manufacturers and suppliers websites to download for free. If this is not the case the manufacturer should be contacted and the information supplied before using the product.
​
Information that should be made available on a Material Safety Data Sheet includes:
Name of the Product
Container size
Identified uses of the product
Supplier details
Emergency contact information
Hazards Identification (9 types)
Flammable, Toxic, Environmental hazard, Serious Health Hazard, Corrosive, Compressed gas, Oxidising, Health hazard/caution and Explosive.
​
For each applicable hazard there should be some greater detail on what the specific hazards are for example:
Galvanising Zinc Spray has the following cautions attached:
​
Extremely flammable aerosol: Use in well ventilated areas away from naked flames.
Pressurised container – may burst if heated: Keep out of direct sunlight or other heat sources.
Causes skin irritation: Use overalls and gloves and a facemask.
Causes serious eye irritation: Use a facemask, visor, googles or safety glasses.
May cause drowsiness or dizziness: Use in well ventilated areas and prevent prolonged exposure. Remove to fresh air and loosen collar if subject is dizzy or drowsy and seek medical advice.
May cause organ damage through prolonged or repeated exposure: Monitor exposure times and implement a policy for medical checks of those at risk of long term exposure.

These cautions should each have a reference in the risk assessment of the substance and recommended methods of reducing or removing the risk. These may be by the use of Personal Protective Equipment (PPE), Respiratory Protective Equipment (RPE) or controlled and limited exposure and the
environment it is used in e.g. outdoor use only.
​
Some data sheets will give details on fire fighting measures and recommended medical responses to exposure by contact with skin, contact with eyes, ingestion or inhalation. The equipment recommended for fire fighting or medical conditions should be available. In the case of an accident concerning a chemical the Safety Data Sheet should be made available to the response unit e.g. fire fighters or medical staff.
​
For every chemical used in a workplace there should be a risk assessment conducted to determine the level of risk it presents to persons, livestock or property. The main risks presented by a product will be listed on its Material Safety Data Sheet. This should be accessible to all persons that use the product and be stored local to where the material or chemical is stored. Material Safety Data Sheets are often made available through manufacturers and suppliers websites to download for free. If this is not the case the manufacturer should be contacted and the information supplied before using the product.
​
Information that should be made available on a Material Safety Data Sheet includes:
Name of the Product
Container size
Identified uses of the product
Supplier details
Emergency contact information
Hazards Identification (9 types)
Flammable, Toxic, Environmental hazard, Serious Health Hazard, Corrosive, Compressed gas, Oxidising, Health hazard/caution and Explosive.
​
Personal Protective Equipment Regulations (PPE) 1992
Personal Protective Equipment (PPE)
​
Where hazards remain after any other control measures have been implemented protective equipment is the last line of defence against injury. PPE equipment comes in a great many forms and must be suitable for the task at hand. It is the employers responsibility to provide PPE where it is required for free. All PPE that is provided must be designed for the associated risk and must bear a CE Mark to ensure it has been tested to prove its suitability. The employer is responsible to provide training/instruction on the use of PPE where required.
​
Any employee that is provided with PPE must use it as per manufacturers' instructions. Any defect or damage to PPE must be brought to the attention of the person responsible for providing the PPE. All PPE should be maintained and stored in a suitable place and be readily available to any employee that requires it.
​

Examples of PPE
​
Hand Protection
Latex Gloves offer light duty protection against liquids, chemicals and oils. Made from natural rubber.
Nitrile Gloves offer Versatile protection from oils, liquids & chemicals. More durable than latex and a suitable alternative for persons with a latex allergy.
Rigger Gloves medium duty glove for general building work fabric backed with soft leather palm originally designed for pulling ropes or cables they are commonplace in construction.
Welders Gauntlets are a heavy leather glove with a high resistance to heat and burning.
Cut Resistant glove offer various levels of mechanical protection from sharp objects.
​
Eye Protection
Safety Glasses offer basic protection against solid foreign objects in front of the wearer.
Safety Goggle offer medium protection against solid foreign objects from all directions.
Face shield offers full face and eye protection from solid foreign objects.
Welding mask protects against extreme light and UV levels produced by welding/cutting metals.
Foot Protection
Safety Trainers offer light protection to toes from impacts. Not suitable for construction site work.
Safety Boot (Steel Toe) offer medium protection to ankles and against impact to toes.
Safety Boot (Steel Toe & Plate) offer ankle protection, impact to toes and stab protection from screws/nails and the like.
Rigger Boots are a full boot offering steel penetration resistant sole, Toe plates ankle and shin protection. Made from leather, suede or mixed man made materials.
Kevlar / composite boots designed for electricians often with a reinforced sole and toe made from impact resistant plastics. Metal free examples have no metallic parts like ferrules or eyelets etc. Often used by security operatives where metal detection is in operation.
​
Hearing Protection
Ear plugs offer light weight protection against dust as well as defence against excessive noise.
Ear Defenders can be banded or clipped to attach to a hard hat and offer high levels of protection against noise at work.
To work on a UK construction site the minimum level of personal protective equipment is usually Safety boots, High visibility vest and a hard hat. Failure to comply is a breach of the health & safety at work act.
Infractions may result in exclusion, fines or in extreme circumstances where injury, death or damage has been incurred prison or blacklisting.
​
The PPE regulations are under the umbrella of the Health & Safety at Work Act and are enforceable by the Health & Safety Executive (HSE).
Respiratory Protective Equipment Regulations (RPE) 1992
Respiratory protection is to protect the user from contaminants in the air or even lack of breathable air. The level of protection must suit the task at hand. All items of certified RPE should have a CE mark. Manufacturer’s instructions will give detailed information on the level of protection provided. The apparatus chosen should have a UK Assigned Protection Factor (AFP) figure.
​
Products are available to protect the user from Very light exposure to large particles to complete isolation from environmental particulates and gases with dedicated breathing apparatus. An assessment of the level of risk and required level of protection should be done before selecting the correct RPE.
​
RPE can be restrictive and/or bulky so consideration should be made for the environmental conditions.

Assigned protection factor AFP What does it mean?
AFP 10 means no more than one tenth of the particulate can make its way into the mask.
AFP 2000 would mean that no more than 1/2000th of the particulate can make its way into the mask or ideally none at all.
Types of protection include:
Face masks
The most basic level of protection against particles. Usually used for very short term low risk operations. Face masks are available up to FFP3 which is suitable for protection from dust and aerosols.
Respirators
They come in half mask or full facemask with visor. They have a replaceable filter usually used for fine particles and some vapours but not gases. Filters have a limited life and should be changed as per manufacturers’ instructions.
Gas Respirators
Filter particulates and gases and have full face masks. The canister or filter has a limited life span and should suit the purpose it is intended for.
​
Breathing Apparatus
Offers the highest level of protection. Examples include supplied air from a source separate from the user (SAR) or when the user has the breathable air in a cylinder on their person (SCBA) e.g. a scuba diver, astronaut or fireman.

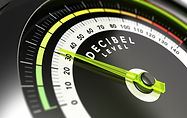
Control of Noise at Work Regulations 2005

These regulations replace the previous Noise at work regulations 1989. The main changes included lowering the safe exposure limit and imposing a requirement for employers to monitor employees aural health where the is exposure to noise at work. These regulations are aimed at employers, employees, self employed persons and trainees. They do not apply to members of the public that chose to go to a noisy area or engage in a noisy activity e.g. home improvements or partying etc.
​
Sound is measured in Decibels and these regulations set the exposure limits and what actions should be taken.
≥80 < 85 db - Lower exposure limit - Where employees may request hearing protection
≥85 db - Upper exposure limit - Mandatory signage required and hearing protection must be worn.
135 - Peak - Lower exposure action value - Risk assess and limit exposure
137 - Peak - Upper exposure action value - Risk assess and limit exposure
140 - Exposure limit - Must never be exceeded
The employer is responsible for assessing the level of risk to employees and must write a risk assessment is exposure is 80db for more than 6 hours, 85db for more than two hours or 90db for more than 45 minutes.
​
The employer is responsible for providing adequate PPE, signage and providing training. The employee is responsible for wearing PPE where required and reporting any defects found.
​
In some cases it is applicable to deem an entire area as a hearing protection zone. In the case signage should be at every entrance and the noise should be contained within that area. All personnel within the zone should have proper safety instruction and have their own hearing protection.
​
Where employees are subject to noise at work a regular health check should be conducted to check that they are not damaging their hearing. This health surveillance should be logged to ensure that no degradation is occurring. The employer should pay all costs and the employee is required to follow any directives given.
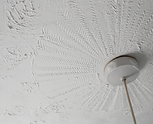
Control of Asbestos at Work Regulations 2009
Asbestos is a fibrous mineral with excellent fire resistance. Once considered to be the wonder building material that could be formed into any shape. Asbestos was used for virtually every part of a building including insulation, pipe lagging, fibre boards, corrugated roofing water tanks, floor finishes, Artex & textured coatings, cisterns, bath panels, & chimney pots etc.
​
Until it was discovered to be a threat to life asbestos was widely used in the UK. In 1985 blue asbestos (Crocidolite) & Brown asbestos (Amosite) were banned. Later in 1992 many of the uses for the less dangerous white asbestos (Chrysotile) were also banned. This means most buildings built or modified between the 1950's and 1992 are likely to have asbestos in one form or another within them.
​
Asbestos is safe if it is not airborne and is not damaged in any way. The dangers arise when the micro fibres are airborne and can be breathed in. With over exposure asbestos can cause a multitude of pulmonary disorders most of which can prove fatal conditions include:
Asbestosis which is a pulmonary fibrosis or scarring of the lungs.
Plural thickening - a thickening of the plural membranes causing pain and breathing difficulties.
Malignant Mesothelioma - An aggressive form of lung cancer
Rounded atelectasis - Fissures in the lung usually caused by one of the conditions above.
Asbestos is deemed responsible for about 5000 deaths per year in the UK and around 90,000 globally. All public buildings should have an asbestos register to identify where asbestos is located in the building. Future building works should take the asbestos register into account so it can be dealt with properly.
​
Only a licensed asbestos contractor can remove and dispose of asbestos anything more than drilling a small hole should be done by a trained licenced contractor. I would recommend any tradesman attend an Asbestos awareness course to better understand this invisible killer. Courses online are around £20.
Blue Asbestos - Crocidolite
Considered to be the most dangerous type of asbestos it has extremely fine fibres and is very brittle so it can be damaged and become airborne very easily. It was often used for roof insulation so if you pop your head up into a loft and notice the insulation is a dark grey/blue or brown (asbestos) instead of bright yellow (glass fibre) then I suggest you leave it to the professionals.
Brown Asbestos - Amosite
Pictured top right in its natural form. This type is as harmful as blue asbestos and for the same reasons. It was extensively used in roofing materials, cement sheets and insulation, cladding and insulation.
​
White Asbestos - Chrysotile
The most abundant of all six types of asbestos it is found in coatings, artex, insulation and the thermal pads in BS3036 semi enclosed rewireable fuses and around arc points on switch gear in older electrical installations.
​
To stay within the guidelines of these regulations, if there is any doubt about the nature of a material that may contain asbestos a survey should be done by a licenced contractor before any work commences that may disturb it.
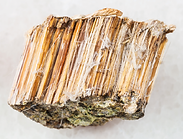
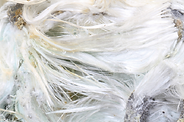
Waste Electrical and Electronic Equipment Regulations

Introduced in 2013 The WEEE regulations made the recycling of electronic and electrical equipment statutory law. WEEE Waste is can be classed as anything that has an electrical or electronic component within it.
​
In the UK we dispose of approximately 2 million tonnes of electrical equipment per year. 40% of the waste is large white goods like cookers and fridges etc. Most electrical equipment contain chemicals that are harmful to the environment and should not be disposed of in simple landfill sites. Leachate from land fill sites can cause damage to the ecosystem and pollute our water supplies. Many electrical goods contain toxic materials like lead, arsenic, mercury, copper, zinc, lithium, HCFC’s, CFC’s, cadmium and PCB’s in older electronic equipment.
​
In some cases the recycling of electrical equipment is down to the manufacturer/supplier which is required to make provision for end of use disposal. If not then the consumer is required to ensure that the equipment is taken to a facility that can deal with EEE Waste. It is an offence to put any EEE waste in a standard municipal waste bin.
​
It should be noted that producers of electrical waste like electricians that are removing old electrical systems need to have a waste carriers licence. This applies to any person that as part of their business produces any kind of waste. Failure to produce a licence when carrying business related waste can result in fines up to £5000. To apply for a WEEE producers licence use the .gov website and fill out an application to the appropriate environmental regulator for your region. Fees vary dependant upon the type of business and how much EEE is produced.
Restriction of Hazardous Substances 2003 (RoHS)
​
This applies to all electrical equipment and its goal is to reduce the use of ten hazardous substances that are commonly found in electrical equipment. It is aimed at the manufacturers of electrical; equipment and is closely linked to the WEEE regulations which are also concerned with reducing the environmental impact of electrical goods. RoHS applies to the following chemicals:
Butyl benzyl phthalate (BBP) Primarily used a plasticiser for PVC
Cadmium (Cd) Televisions, electroplating and batteries
Dibutyl phthalate (DBP) Primarily used as a plasticiser
Diisobutyl phthalate (DIBP) Primarily used as a plasticiser
Hexavalent chromium (Cr6+) Used in protective and decorative coatings
Mercury (Hg) Used in fluorescent lighting and switches
Polybrominated biphenyls (PBB) Flame retardant additive to plastics
Polybrominated diphenyl ether (PBDE)Bis(2-ethylhexyl) phthalate (DEHP) is a flame retardant plastic additive.
​
RoHS is an EU Directive and individual countries within the EU are able to use it as a guidance document and implement it in their own way. From 2023 compact fluorescent and fluorescent tubes will have production phased out. LED alternatives are already in production.
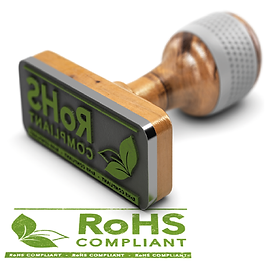

Provision & Use of Work Equipment Regulations (PUWER) 1998
These regulations govern the use of equipment by employed, self employed or persons supervising work activities that require the use of equipment. Use of includes starting, stopping, programming, setting, transporting, modifying, maintaining servicing and even cleaning. The regulations apply to ALL equipment new, second hand & existing from before the enforcement of these regulations.
Any machinery that does not comply with these regulations should be removed from service or modified to meet the regulations before further use.
​
No work equipment should pose an unacceptable risk to the user or any other persons. A simple example would be a circular saw with no guard. This could be remedied by the fitting of a guard but until that is done it would be an unacceptable risk to the user.
​
There must be adequate space and lighting for the use of any piece of work equipment which may require temporary lighting in the case of mobile or transportable equipment. Where machinery is run by a combustion engine adequate air quality needs to be provided for persons in the vicinity.
​
Regulation 5 refers to maintenance of work equipment. A Register should be kept for machinery detailing maintenance checks and its suitability to remain in service.
​
Regulation 6 refers to Inspection - All machinery should be regularly inspected to ensure it is fit for purpose. Portable or hand held appliance should have a Portable Appliance Test (PAT) done and be labelled to detail when and by whom it was tested. For fixed machinery manufacturers instructions should detail the recommended checks to be performed. For information on how to test portable appliances for safety see the testing section of this book.
​
Regulation 7 refers to competency. All users of work equipment should be competent, adequately trained & experienced or sufficiently supervised by a competent person. A simple control measure for machinery would be to provide keyed control for competent persons. Where training is required and given a log should be made to monitor who is competent.
​
Regulation 8 expands upon the Health & Safety at work regulation that requires employers to prove adequate information or instructions. In the case of machinery this may be an instruction manual or notices where required. This information should be accessible to all users of the equipment.
​
Regulation 9 refers to the requirements for training users of work equipment. If training is required it should be given before using the equipment. If formal qualifications or licences are required these should be checked before the person operates the equipment. For larger companies copies of all formal qualifications and licences may be a good way of ensuring compliance.
​
Regulation 10 refers to conformity to European standards. If a machine has a valid CE mark on it should conform to European standards. including the machinery directive, PPE Directive, Pressure equipment directive & simple pressure vessel directive. New equipment should also have a copy of the EC declaration of conformity.
​
Regulation 11 refers to protecting persons from dangerous part of machines. Rotating machines and other moving parts that could cause harm should have suitable guards to prevent accidental contact. Alternatively the moving part should be stopped before a person came come into contact with it. This may also be achieved by the use of protective appliances for example a simple push stick to prevent accidental contact with sharp tooling or blades.
Use the .gov link above to read the full HSE Guidance Document on PUWER 1998.
Manual Handling Operations Regulations 1992 (2002)
The Health & Safety Executive (HSE) publishes figures for work related musculo-skeletal disorders each year. Currently 6.9 million working days are lost per annum and an average of 13.8 days for each reported disorder. This is an improvement over the last 20 years due to improved legislation and staff training. The manual handling operations regulations plays a big part in that.
It is stated in regulation 4 that where possible it is preferred that there are no manual handling operations. It is not reasonably practicable for this to be the case in all types of work especially as an electrician. The regulations are in place to minimise risk and protect the employee with a statutory law.
​
Where manual handling is a standard operation a risk assessment should be made and an associated method statement to inform on the best possible method to minimise risk of injury. Employees involved in the manual handling are required by regulation 5 to adhere to any safe system of work or method statement that has been prepared by the employer. Risk assessments should be periodically checked to see if they are still effective.
​
It is mandatory for employers to train their staff in the use of lifting aids where required and to instruct on how to safely lift and move objects in the workplace. Employers must provide equipment where necessary to remove or limit manual handling operations where the employee may come to harm.
​
Where possible an objects weight should be displayed and if there is a heavier side. For example older monitors are heavier on the glass screen side. Heavy items should not be stored at height unless they are on a racking system that is designed for access by manual handling aids like a fork lift or appropriate working platform.
​
When moving objects you should determine a safe route before the lift to establish there are no unexpected hazards or obstacles. There should be adequate lighting especially if stairs are involved.
When picking up an object from the floor ensure it is not too heavy for you to lift. There is no defined maximum weight as every person is different.
You should know your limits and not lift near the upper end of that limit.
​
Lifting Method
Stand over the object with your feet shoulder width apart. Bend at the knees and grip the object securely. Lift using your legs and knees NOT your back. Hold the weight close to your body and do not twist during the lift. When moving turn with your feet not your waist. If the weight is too heavy or bulky then seek assistance or use an appropriate manual handling aid like a sack truck or trolley.
If there is any doubt whatsoever that the load can be managed safely then do not attempt the lift.
​
Lifting aids include:
Pulleys, fork lift trucks, trolleys, sack trucks, pallet trucks, levers, conveyors, hoists, wheel barrows, suction pads, jacks, harnesses, winches, ratchets, mobile work platforms, inflatable pads, dumb waiters, gurneys, stretchers & specialised equipment etc.
The choice of equipment employed should be made following manufacturer's specifications, recommendations and with adequate training & experience.
​
A free copy of the HSE guidance is available by clicking the .gov link above.
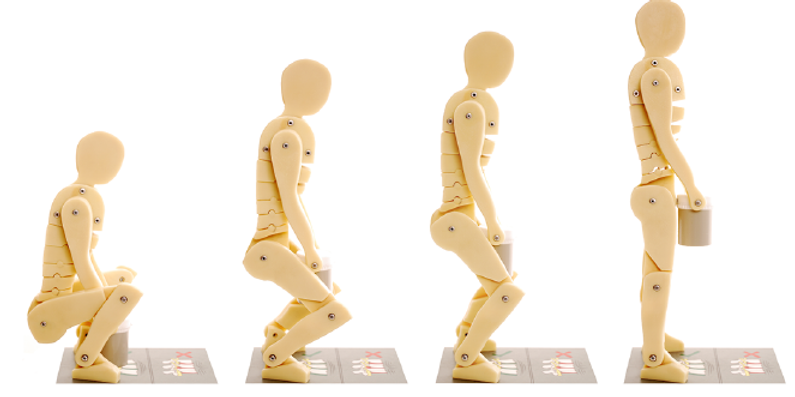
Health & Safety (First Aid) Regulations 1981

In all workplaces there must be provision to provide at least basic first aid in the case of an accident at work where the person may or may not need further assistance from a medical practitioner. First aid can prevent minor injuries from becoming major injuries or even prevent death in severe cases. The employer should provide an adequate number of trained first aid personnel for the purpose of administering first aid treatment. The HSE (Health & Safety Executive) recommend at least one trained first aider for companies with 5-50 employees and at least one more for every further 50 employees. If the company has satellite buildings or is a very large spread out complex this should be considered to provide good coverage of first aid facilities.
​
The standard accepted entry level of training is the four day First Aid at Work qualification which is delivered all across the UK by the Red Cross or St John's Ambulance and other organisations. The HSE recommends that every practitioner does the 2 day refresher course every year and repeat the four day training course every three years. This is to maintain skill levels, deal with gaps in memory or bad habits and disseminate new methods being used in first aid situations.
If there is specialist equipment for the purpose of first aid like hoists, defibrillators, breathing apparatus etc then there must be a designated person that is trained in its use. The minimum first aid equipment should at least be a standard first aid kit and an eyewash station with a suitable location for hygienic use of. There should be a designated person who is responsible for maintaining the first aid stock levels and keeping stock in date where required.
​
If the workplace has higher level of risk of hazards or very specific hazards a first aid room may be required and pre-warning the emergency services of the specific hazard. For example storage of corrosive substances that may cause injury in an accident. A designated first aid room must have adequate access/egress for a stretcher and bearers. It must also be clearly signposted using the correct green/white signage.
​
Companies must keep a record of accidents and the administering of first aid to build a picture of where extra control measures may be required. Conducting risk assessments to help identify the causes of more serious accidents or repeated accidents should be considered e.g. common cuts to hands may be remedied by the provision of gloves or guards or a change of method. The accident book records must be kept securely as they contain personally identifiable data protected by General Data Protection Regulations (GDPR).
Risk assessments and associated method statements must be available to all employees that may be harmed by any highlighted activity that has a risk attached.
​
The accident book records should have the following information as a minimum:
​
-
Date, time and location of the incident
-
Name and job title of the injured or ill person
-
Details of the injury/illness and what first aid was administered
-
What happened to the person immediately afterwards (e.g. went back to work, home / hospital)
-
Name and signature of the first-aider or person dealing with the incident.

RIDDOR - Reporting of Injuries Deaths and Dangerous Occurrences 2013
When a death, disease, injury or dangerous occurrence happens in the workplace and is work related it should be reported to the HSE using the .gov portal (https://www.hse.gov.uk/riddor/report.htm). The responsibility is down to the employer or designated person assigned that duty by the employer.
Not all incidents need to be reported so here is a non-exhaustive list of reportable occurrences:
-
Any work related death
-
Injuries from a work based activity that result in seven or more days off work
-
Injuries to non workers which result in them being taken to hospital
-
Diagnosed cases of industrial diseases
-
Certain dangerous occurrences that have the potential to cause harm
​
Injuries that should be reported include:
​
-
Fractures to bones other than fingers, thumbs or toes
-
Amputation of any body part
-
Sight loss or damage from a work activity
-
Organ damage from a crush injury
-
Burns that affect organs sight or more than 10% of the body
-
Removal of scalp enough to require a hospital visit
-
Unconsciousness caused by lack of oxygen or injury
-
Injuries from confined spaces requiring >24 hours in hospital including hypothermia, hyperthermia or any condition that required resuscitation
-
Industrial diseases that are reportable are:
-
Cancer caused by a work activity e.g. Mesothelioma from exposure to asbestos
-
Severe cramp of the forearm or hand
-
Carpal tunnel syndrome
-
Hand-arm vibration
-
Occupational asthma from breathing in fumes, gas or particles at work
-
Dermatitis from work related activities
-
Tendonitis or tenosynovitis of the hand or forearm
-
Diseases caused by exposure to biological agents at work e.g. Legionnaires' disease
​
Dangerous Occurrences that should be reported include:
​
-
Structural collapse or overturning of any part of a lift or lifting equipment
-
Plant or equipment hitting overhead power lines
-
Fires or explosions causing work to be stopped for more than 24 hours
-
Collapse of a fixed scaffold or suspended scaffold
-
Failure of a pressure vessel that causes an explosion
​
In all cases you may fill in a form online or in major cases especially work related deaths the HSE can be directly by calling 0845 300 9923
​
If you are employing 5 or more people you should have a health and safety policy and in the policy it should state who is responsible in the case of a reportable incident.
​

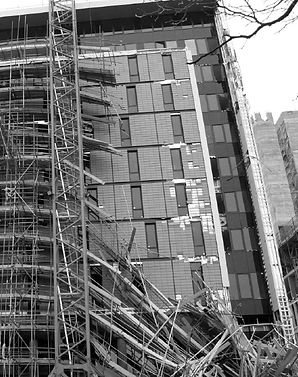
Electricity at Work Regulations
Scope:
A Statutory document to prevent damage or danger to buildings, persons or livestock from electricity at work. The Act is under the umbrella of the Health & Safety at Work Act.
​
In very short form some of the main regulations include:
​
Regulation 3 - The regulations apply to all employers, employees and self employed persons.
​
Regulation 4 - The electrical system must be maintained to ensure it is fit to stay in service (periodic inspection)
​
Regulation 5 - The electrical system should be of sufficient strength regarding its capability to carry the expected currents, electro-magnetic effects & heat. Protective devices should be capable of disconnecting the highest possible fault current that may be experienced by the system.
​
Regulation 6 - The system must be design and installed to deal with any prospective adverse effects of its environment. This includes ingress of foreign solid bodies or moisture (IP rating)
​
Additional effects including but not limited to:
-
Heat
-
Electromagnetic effect
-
Stress
-
Mechanical damage
-
Chemical effects
-
Corrosion
-
Explosive atmospheres
-
Vibration
-
Flora and Fauna
-
Earthquakes / seismic activity
​
Regulation 7 - All live parts should either be contained or have precautions in place to prevent accidental contact with a live part. Methods include insulation, containment, placing out of reach or placing barriers or obstacles.
​
Regulation 8 - Earthing or other suitable precaution regards the protection of property, persons or livestock in fault conditions. The most common method is earthing bonding and the use of circuit protective conductors to carry fault currents safely to earth and cause automatic disconnection of the supply. Other methods include extra low voltage double or reinforced insulation or electrical separation
​
Regulation 9 - Integrity of referenced conductors - Mostly applicable to PME systems where neutral and earth have combined functions.
​
Regulation 10 -Integrity of Connections
​
Regulation 11 - Protection against overload / short circuit currents
​
Regulation 12 - Means of isolation for all distribution and final circuits.
Regulation 13 - Precautions for equipment made dead (Safe isolation procedure)
​
Regulation 14 - Work on or near live conductors - Not to be done unless it is unreasonable or practicable not to do so. In that case the person should have suitable knowledge and equipment to keep them safe from danger.
​
Regulation 15 - Provision of adequate working space and lighting where electrical equipment may be accessed, installed or maintained.

Non Statutory Documents
Non Statutory Documents are for guidance on how to work within the confines of a Statutory Document. Their main purpose is to make plain what the requirements are and how to work within that frame work.
​
Electricians and anyone working around electricity at work should have a basic knowledge of the requirements of the Electricity at work regulations.
​
On the left is a link to HSR25 which is a HSE publication on the requirements set out by the electricity at work regulations. The PDF version is free to download.
​
BS 7671 Gives detailed information on how to remain in line with the electricity at work regulations. I have included a section on this site with a detailed look at BS7671 follow the link below.